Revitalization | Haitian Die Casting Officially Launches Magnesium Alloy Injection Molding Equipment
2022-07-12
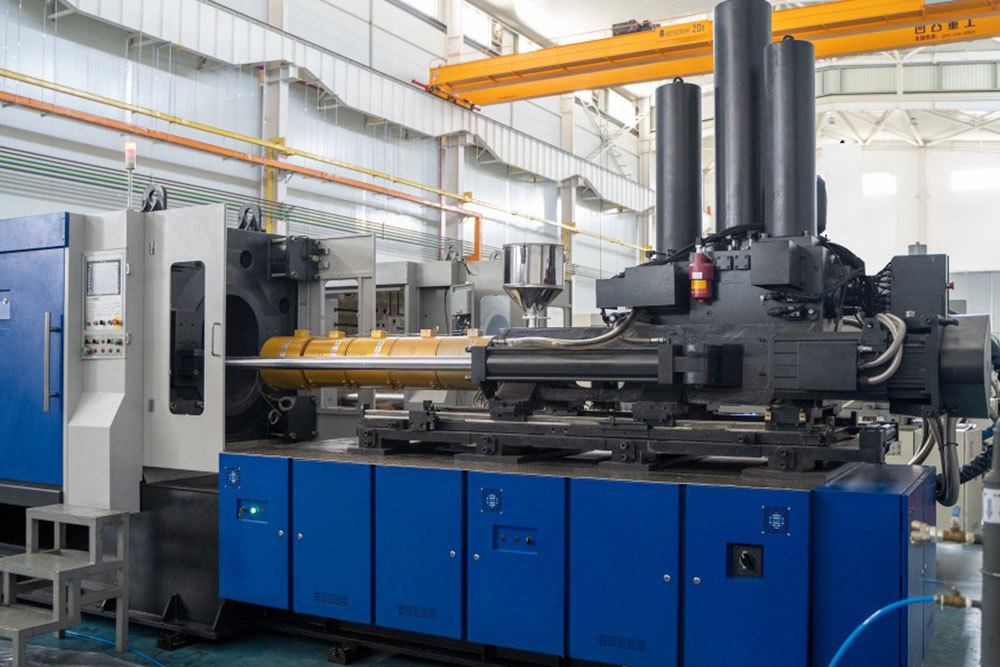
Under the “carbon peaking and carbon neutrality” goal, automobile lightweight has become an important development direction for major car companies. Among the lightweight materials, magnesium alloy has significant advantages, its density is only 2/3 of aluminum alloy, and it has good strength and rigidity, which is very conducive to the design of the overall component. In particular, medium and large, complex and precision magnesium alloy parts will gain huge market prospects.
Compared with high-pressure die casting, magnesium alloy products produced by injection molding have higher accuracy, better mechanical properties, longer mold service life, and safer, more energy-efficient, and more environmentally friendly production processes.
“Revitalization” Release in Shock
By introducing all of SSD’s patents and technologies in the magnesium alloy semi-solid field and integrating the application accumulation of Haitian Group’s injection molding machines and die casting machines, Haitian Die Casting has concentrated on research and development, made great efforts to build and launched the HMG magnesium alloy injection molding machine, officially entering the magnesium alloy injection molding equipment market. At present, the models that can be mass-produced are 300T, 700T, 850T, 1300T, and 2500T.
Create a “high quality standard” for HMG
Next, let’s decode the HMG magnesium alloy injection molding machine created by Haitian Die Casting:
HMG models are based on the key patented technology and market application experience of 16 years of magnesium alloy injection molding and supported by Haitian Group’s world leading injection molding technology, equipment manufacturing experience and Haitian Material Research Institute. Driven by the double engine of joint research and development and independent innovation, Haitian Die Casting’s technical team created a new product HMG series – magnesium alloy injection molding machine in just one year.
In terms of product positioning, HMG series will move towards the international advanced magnesium alloy injection molding equipment, comprehensively highlighting the product development concept of “high quality standards”.
Strategic signing
On June 29, Millison Technology and Haitian Die Casting signed the Strategic Cooperation Agreement on Mass Purchase and Joint Development of Large Die Casting Machine and Magnesium Alloy Injection Molding Equipment. According to part of the agreement, Millison Technology will purchase five 1300T and three 2500T magnesium injection molding machines from Haitian Die Casting.
The strategic cooperation between Millison Technology and Haitian Metal will further enhance Millison Technology’s hard power in manufacturing equipment and accelerate its development speed on the track of magnesium alloy products. The Parties will open more comprehensive cooperation and jointly promote the new trend of industrial development.
Jiang Hanjin, Vice President of Millison Technology, and Le Xiaodong, General Manager of Haitian Die Casting
At the ceremony, Millison Technology and the National Magnesium Center of Chongqing University signed the Technical Cooperation Agreement on the Development of Super Large Automotive Body Structural Members to jointly develop lightweight magnesium/aluminum alloy super-large automotive body structural members, and strive to promote the large-scale, integrated and lightweight manufacturing of new energy vehicle parts faster, promote the realization of the dual carbon strategy, and lead the new era of automobile lightweight.
Ma Minghai, Executive Vice President of Millison Technology, and Jiang Bin, Executive Deputy Director of the National Magnesium Center of Chongqing University
As a key new industry under the Group, Haitian Die Casting has received all-round support and guarantee from the Group’s technology accumulation, manufacturing platform and quality system, quickly laying a solid foundation. Constantly overcoming difficulties, Haitian Die Casting provides customers with leading technology and reliable quality aluminum magnesium alloy forming solutions, and provides more innovative contributions to the development of automotive lightweight.